Design of Ball Valves Used in Pipelines
Design of ball valves used in pipelines requires high safety and reliability. The idea should be implemented in the whole process, including design, process specification, parts processing, type testing, product testing, quality control and after sales. Both long pipelines and urban pipelines nets are energy supply lines and also national economic lifelines. Just like power distribution networks on ground, global underground oil and gas transmission pipelines are also the bases for urban industries and home application.
Design of body is classified into full welded design and split design.
Full welded body is designed into tubular structure or ball structure. Tubular structure has double weld joints. The structure has large heat imput, complicated residual stress, and large axial and radial direction deformation. Ball structure has four weld joints. For technology development, middle single weld joint can be welded directly into mold by using right and left body hot forging molding, reducing heat imput and decreasing axial and radial direction deformation.
In general, split structure consists of body and left and right connector. Connectors are connected with body by bolts. The thickness of connecting flanges and joint strength of bolts should be designed according flanges which corresponding to inner diameter of body. The joint strength should prevent connection of pipelines from loosing due to stress, which results in sealing efficacy. Body contacts with connector by face-to-face. Gas does not exist. Sealing should meet the requirements of fire safety. Use rubber O-ring and twining metal gasket to form sealing. The materials of body are forge pieces. When temperature above -29C°, ASTM A105 is used. When temperature below -29C°, ASTM A350 LF2 is used. In terms of welded body, there should be other limitations on chemical components, carbon content, carbon equivalent, sulfur or phosphorus contained in A105 or LF2. Forge pieces are checked based on three-level forge piece standard and 100% lossless flaw detection is carried out. Dyed check and ultrasonic flaw detection are carried out on weld joint.
Sealing socket and sealing seat adopt composite sealing structure – metal to metal sealing, preventing solid particles from entering. Use rubber, PTFE plastic, nylon, PEEK and other soft sealing materials as secondary sealing for ensuring zero leakage. However, foreign matters may be imported into pipelines unexpectedly, damaging soft sealing materials. Nevertheless, ball valves used in pipelines is equipped with injection system for emergency sealants, to meet temporary sealing requirements.
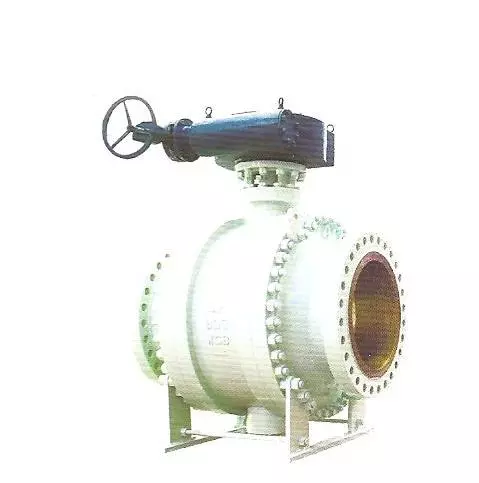